
How is it manufactured?
- 1 furnace - 80Tn per day - 14.000Tn per year
- 1 automated assembly line + flexible semi-automatic line - Max 4M insulators.
- 1 automated RTV spray coating line.
- ISO 17025 accredited laboratory
- More than 150 employees in the business unit
Suspension insulator components
- Dielectric: One dielectric made of toughened glass with the appropriate properties and shape for the specified mechanical rating and the environmental conditions in which it must function.
- Cap: One hot-dip galvanized cast iron cap. It is marked with our brand name “ESA” and with the other engraved and inked marks required by the applicable standards to keep a correct identification and individual traceability.
- Pin: One hot-dip galvanized forged steel pin. It may come with anti-corrosion zinc sleeve (sacrificial anode) when requested. This zinc sleeve is strongly recommended for insulators which are going to be used in heavily polluted environments.
- Aluminous Cement: The cap and the pin are assembled on the glass piece using aluminous cement with the appropriate properties to withstand the thermomechanical efforts.
- Split pin: Lastly, the insulator cap has a stainless steel or phosphor bronze locking device (split pin) which secures the coupling units.
DIELECTRIC MANUFACTURING
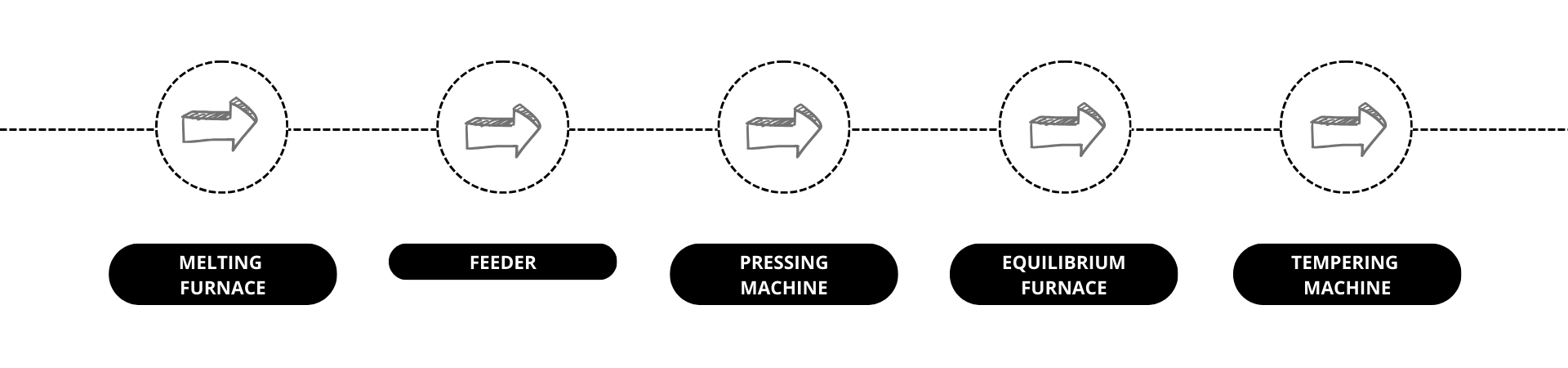
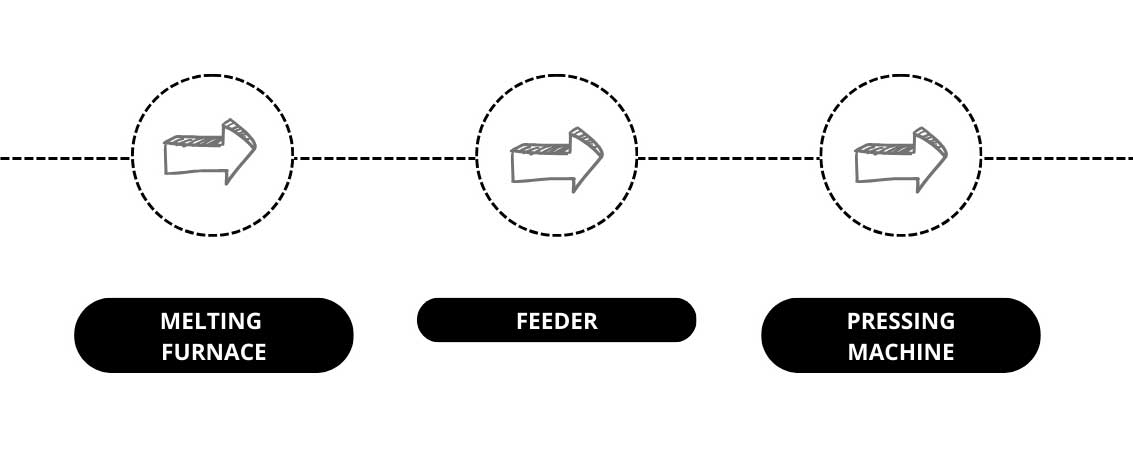
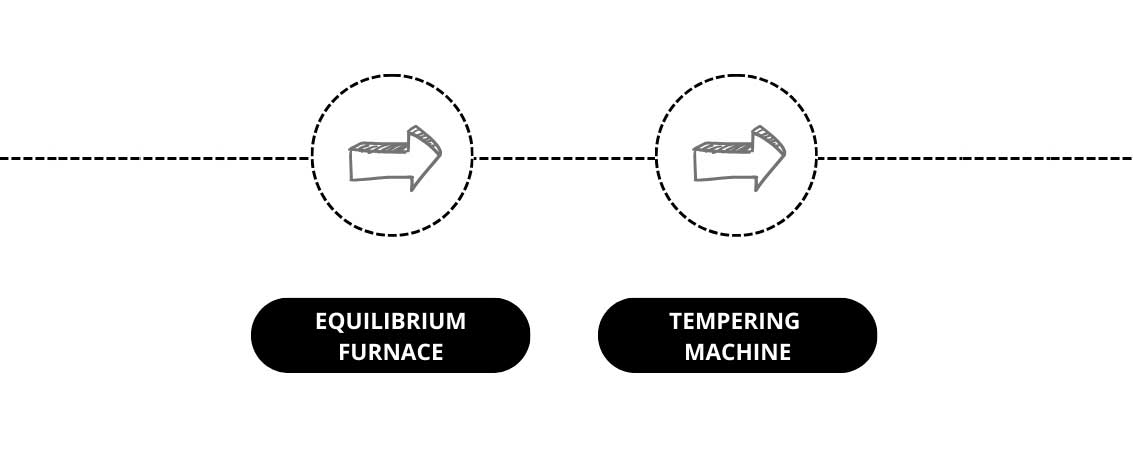
- Melting Furnace: The raw material is introduced into the furnace to be melted and then it is allowed to pass through the feeder channel(s) to transport the glass from the furnace to the pressing machine.
- Feeder: Its functions are to transport the glass to the pressing machine, to condition the glass in temperature and, in its final part, to dispense portions of glass to be produced. Once we have obtained a portion of glass determined by the model being produced, a blade mechanism will be used to cut/separate it from the mass of the feeder channel. Through this process the glass will drop by its own weight into the molds that will be placed in the press.
- Pressing Machine: By means of a hydraulic pressing system we conform the shape of the glass piece (dielectric). After this process, it will be conditioned in temperature to be able to temper the glass. In case of not being able to ensure the correct temperature, the pieces will be introduced into an equilibrium furnace to equilibrate the temperature of all parts of the piece.
- Equilibrium Furnace: To ensure that the entire piece of glass has a homogeneous temperature, 100% of these pieces go through an equilibrium furnace prior to tempering.
- Tempering machine: In this equipment we generate the tensions in the glass. These tensions are essential to guaranteee that the dielectric will withstand the tensile and compenssive stresses to which it will be subjected in the supply lines.
THERMAL SHOCKS
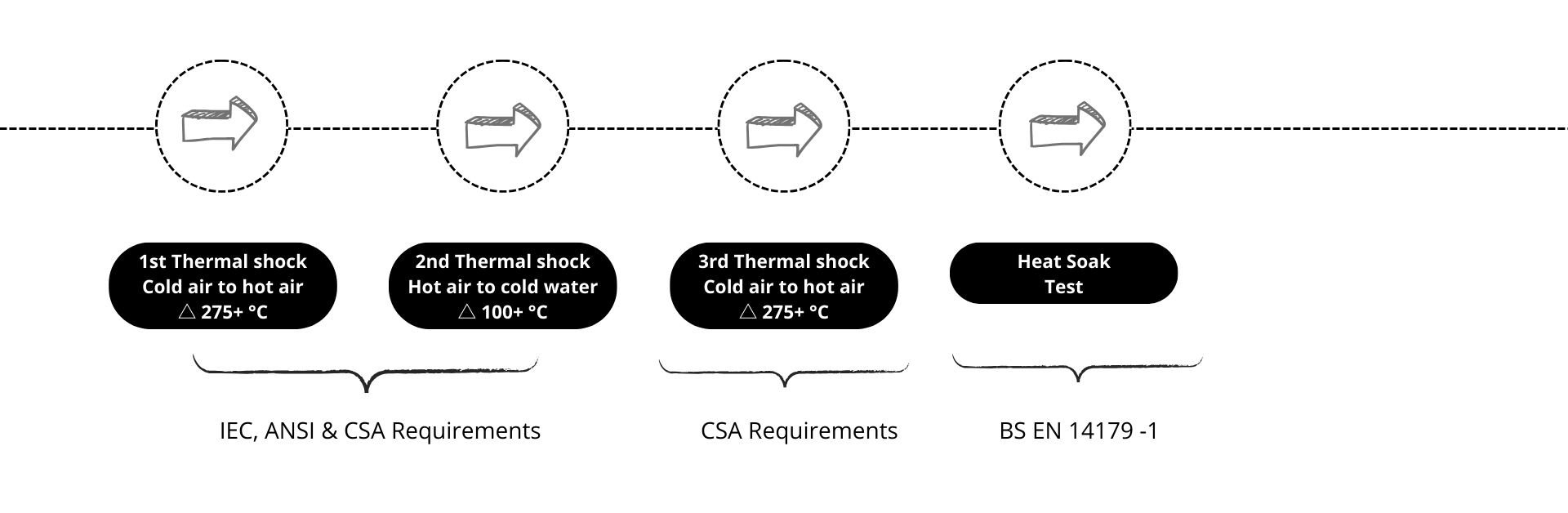
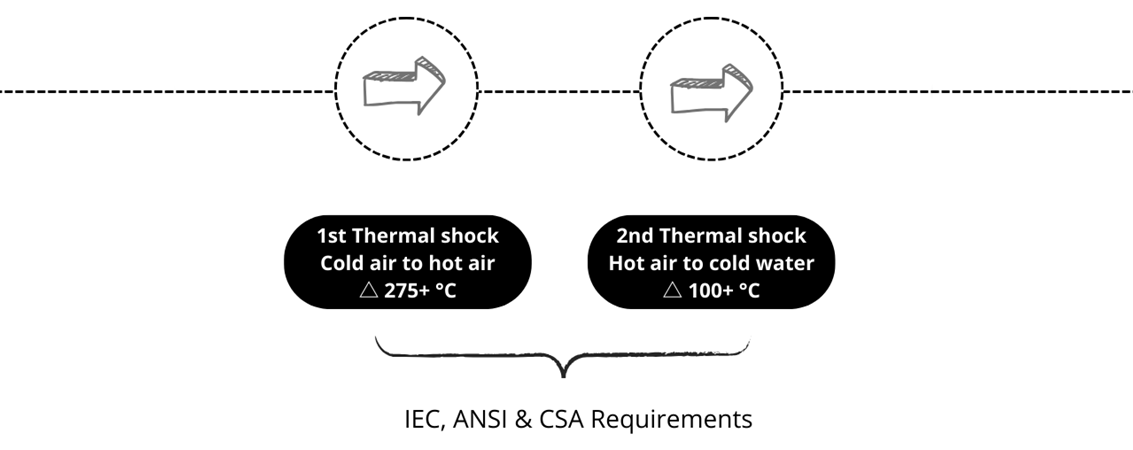
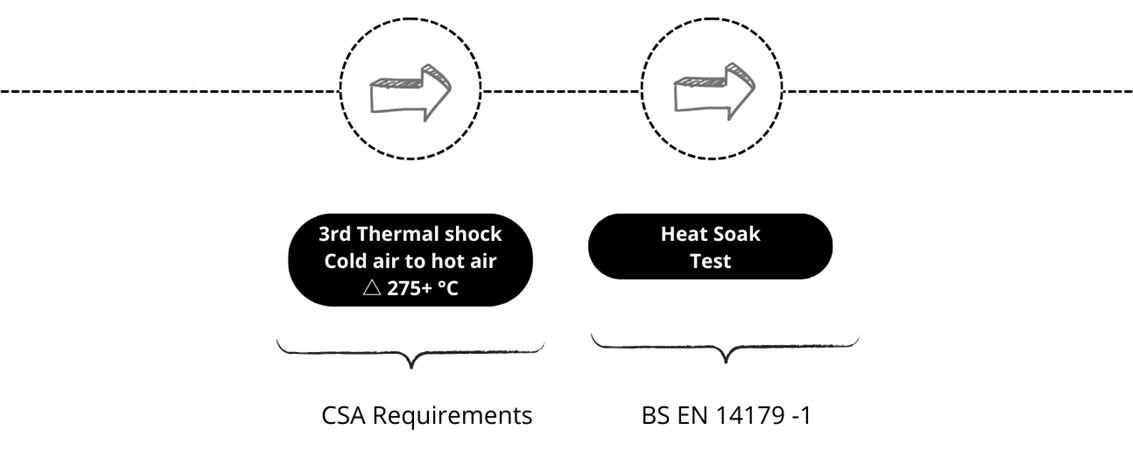
Before assembling with their metal components, all the shells of toughened glass insulators are subjected to a series of thermal shocks as routine tests, as follows:
- Cold-to-hot shock: each toughened glass shell is quickly brought from ambient temperature to a temperature at least 300 °C higher and maintained at this high temperature for at least 1 min.
- Hot-to-cold shock:each toughened glass shell is quickly and completely immersed in water at a temperature not exceeding 50 °C; the shells have been preheated by hot air or other suitable means to a uniform temperature at least 100 °C higher than that of the water.
- Cold-to-hot shock: the cold-to-hot thermal shock specified in Item a) is carried out for a second time.
- Heat Soaking: in order to eliminate any risk of explosion by nickel sulphide inclusions (which can cause the glass to shatter after production of the insulator), after the second cold-to-hot thermal shock, each toughened glass shell is maintained at 250 ºC for 2 hours.
INSULATORS ASSEMBLY
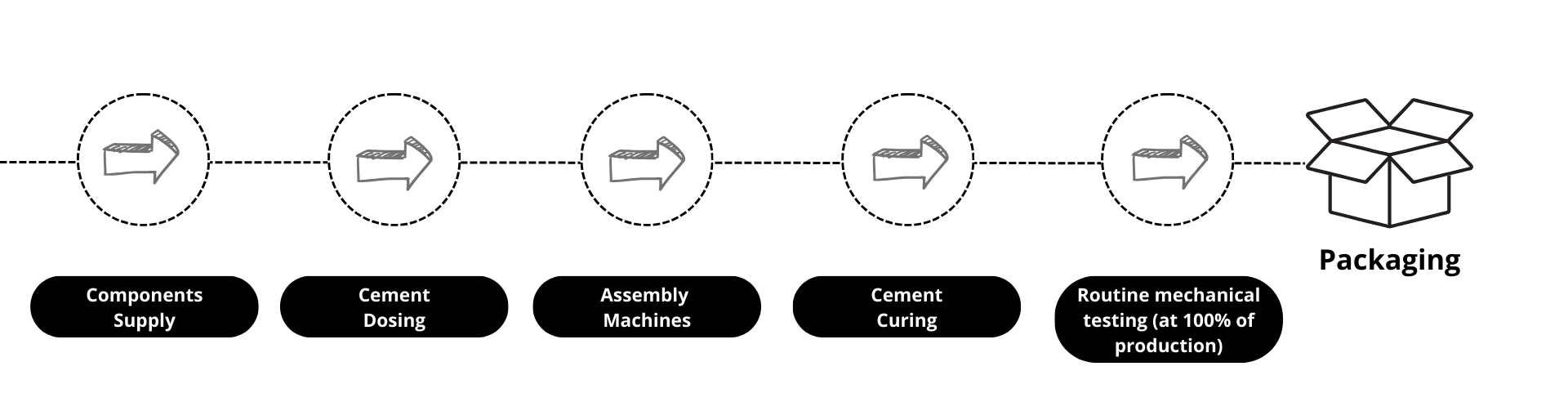

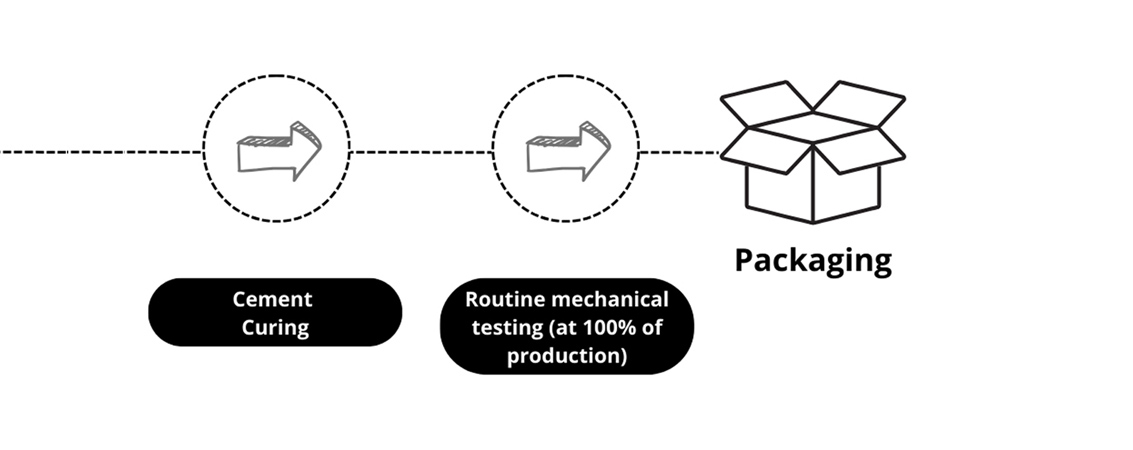
- Component supply: : In this first step, the necessary components for the glass insulator are procured and verified, which generally include the dielectric, cap, pin and split pin.
- Cement Dosing:Cement is carefully dosed to ensure a proper assembly. It acts as a bonding agent that will hold the insulator parts together. We use 100% alumina cement, which is immune to cement growth expansion phenomena.
- Assembly Machines: The insulator parts are assembled in specific machines that apply the cement homogeneously and ensure a solid bond. This involves attaching the cap and pin to the of the dielectric.
- Cement Curingt: After assembly, the insulators are placed in a curing water tank where the cement hardens, and the stability of the bonds is ensured. Curing time and conditions are critical to the final strength of the insulator.
- Routine Mechanical Testing (to 100% of Production): Each assembled insulator undergoes routine mechanical testing and visual inspection, which ensures its quality and strength. This is done to ensure that each insulator meets design specifications and is safe for use in electrical applications.
- Packaging: Once the insulators have passed the quality tests, they are suitably packaged for distribution and delivery. Packaging must protect the insulators from damage during transport and storage, and often includes safety measures to prevent breakage of the glass.